Unlocking the Power of Steel Stamping: Techniques for Boosted Item Advancement
In the world of manufacturing, the utilization of metal marking holds a substantial location due to its flexibility and effectiveness in generating elaborate components and components. The true potential of steel stamping continues to be untapped by numerous firms seeking to boost their product advancement procedures. By checking out sophisticated techniques and strategies tailored to maximize design, material selection, manufacturing efficiency, and high quality control, organizations can unlock a riches of possibilities to raise their products to brand-new heights of innovation and efficiency.
Advantages of Metal Stamping
Metal marking deals a effective and cost-efficient method for creating premium steel parts. This production procedure entails shaping, cutting, or forming metal sheets utilizing a marking press (Metal Stamping). Among the key benefits of metal marking is its capability to develop complicated geometries with high accuracy and consistency. This is especially useful for sectors such as automotive, aerospace, and electronics, where detailed steel components are frequently needed.
Additionally, steel marking permits for high-volume manufacturing, making it ideal for tasks that call for huge quantities of steel components. The rate and repeatability of the stamping procedure not only ensure cost savings yet additionally add to faster turnaround times for manufacturing orders. In addition, making use of automated tools in steel stamping helps minimize the risk of human error, leading to boosted general product quality.
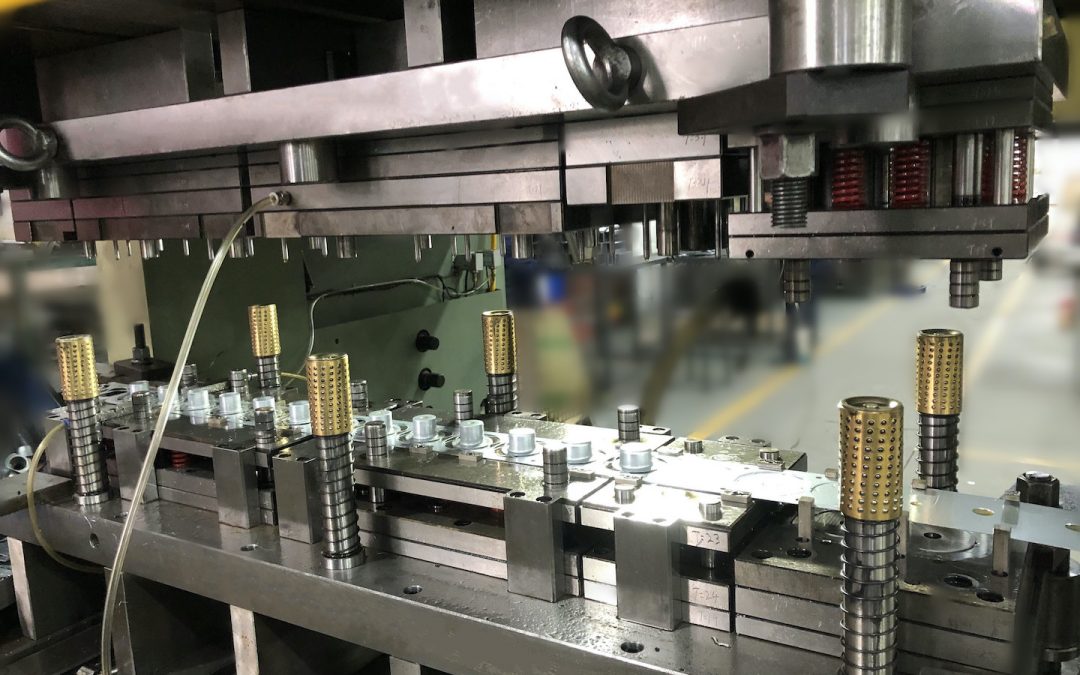
Layout Optimization Methods
Through careful consideration of product properties and geometric arrangements, design optimization methods play a critical function in boosting the effectiveness and capability of steel stamping procedures. By tactically assessing elements such as material thickness, kind, and toughness, producers can customize the layout to take full advantage of the efficiency of the marking procedure. Utilizing simulation software application, engineers can anticipate exactly how different layout variations will certainly act under numerous marking problems, permitting for the recognition of potential issues prior to production begins.
Additionally, integrating functions like fillets, chamfers, and embosses into the design can improve the total top quality of the stamped part while lowering the threat of flaws such as splitting or contorting. In addition, maximizing the format of attributes on the component can improve the material flow throughout marking, causing even more regular and specific results.
Fundamentally, layout optimization techniques enable suppliers to fine-tune their metal marking procedures, causing enhanced product top quality, boosted production effectiveness, and eventually, a much more competitive placement in the marketplace.
Product Choice Techniques
Layout optimization methods in metal stamping processes heavily depend on critical material choice techniques to ensure the preferred performance and effectiveness of the manufactured components. The option of product in metal marking is essential as it directly affects the quality, durability, and general performance of the end product. When picking the suitable product for a specific project, aspects such as mechanical properties, corrosion, formability, and cost-effectiveness resistance must be considered.
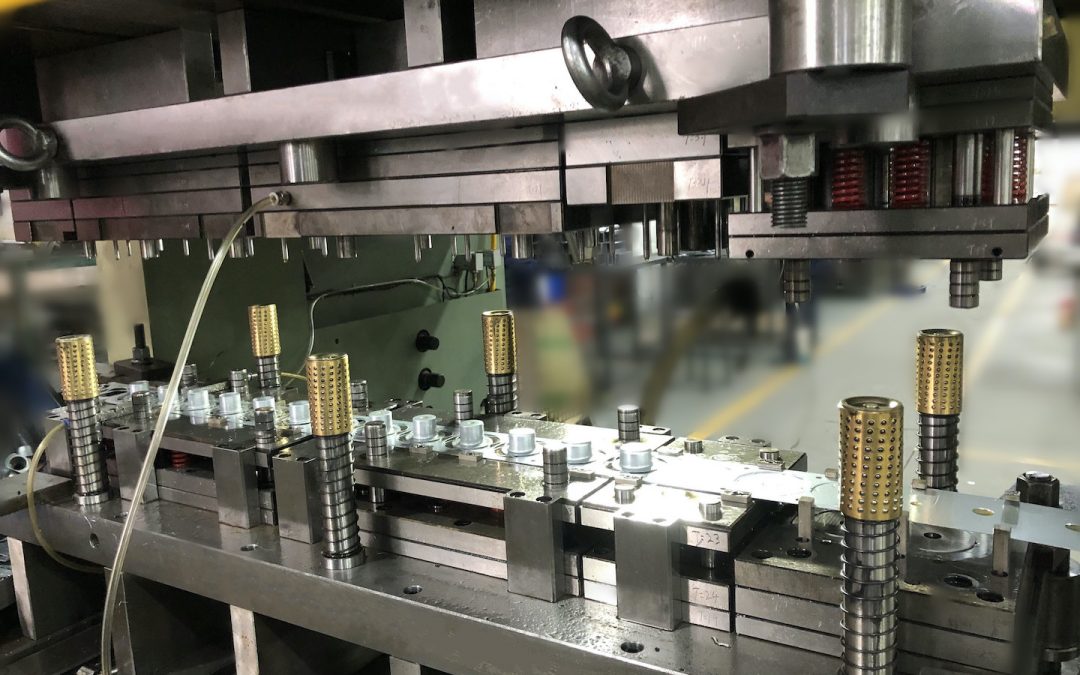
Balancing the efficiency requirements with the general cost of materials is vital to ensure the economic stability of the manufacturing procedure. By thoroughly evaluating these elements, suppliers can optimize their product option approaches to attain superior item high quality and functional performance.
Enhancing Manufacturing Performance
Efficiency in production procedures is a crucial aspect for making certain cost-effectiveness and prompt distribution of top quality metal marked components. To improve production efficiency in metal marking, numerous methods can be carried out.
Furthermore, executing automation and robotics in steel marking procedures can considerably enhance efficiency and consistency while reducing labor costs. Automated systems can execute repeated tasks with high accuracy and speed, leading to boosted manufacturing effectiveness and higher result prices. Spending in contemporary stamping devices with advanced attributes, such as servo-driven presses and fast die change systems, can better enhance production procedures and reduce downtime.
Additionally, developing clear communication networks and fostering partnership between production, style, and design groups is critical for determining possible bottlenecks and carrying out continuous renovations in the manufacturing workflow - Metal Stamping. By accepting lean production principles and leveraging technology developments, suppliers can unlock the full capacity of metal stamping procedures and attain higher manufacturing performance
Top Quality Control and Evaluation Techniques
To guarantee the regular production of premium metal stamped parts, rigorous blog quality control and examination approaches play an essential role in verifying the accuracy and stability of the manufacturing procedure. Quality control in steel stamping includes a collection of organized checks and steps to assure that each part satisfies the specific needs. In addition, progressed innovations such as automated optical inspection systems and coordinate determining makers are progressively being made use of to enhance the accuracy and effectiveness of top quality control processes in steel marking.
Conclusion
In final thought, steel marking deals various advantages such as cost-effectiveness, accuracy, and versatility in product advancement. By implementing design optimization methods, choosing ideal products, and boosting manufacturing efficiency, makers can accomplish better products with decreased lead times. Quality assurance and evaluation methods play an essential function in making certain the last items meet the required criteria. On the whole, opening the power of steel marking requires a calculated approach to improve item advancement processes.
Steel marking offers a reliable and economical method for producing top quality steel elements.In addition, metal stamping permits for high-volume manufacturing, making it suitable for tasks that call for large amounts of metal components.Through mindful consideration of product homes and geometric configurations, style optimization techniques play an why not try these out essential duty in improving the efficiency and capability of steel stamping procedures.Layout optimization techniques in steel marking processes heavily depend on tactical product selection approaches to make certain the preferred efficiency and effectiveness of the manufactured components. The choice of product in steel stamping is vital as it directly influences the top quality, longevity, and general capability of the final item.